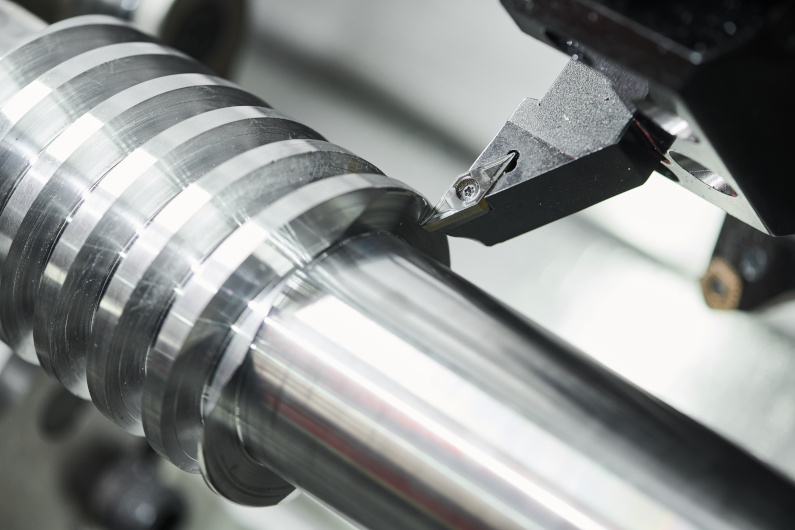
CNC machining has changed the manufacturing industry, offering precision and efficiency in producing complex parts. Among the materials commonly machined, stainless steel stands out for its strength, corrosion resistance, and aesthetic appeal. However, machining stainless steel poses unique challenges due to its material properties.
This article explains the diferent challenges associated with CNC machining of stainless steel and discuss effective solutions to these challenges.
What Is CNC Machining Stainless Steel?
CNC machining stainless steel refers to the advanced process of using computer-controlled machinery to precisely cut, shape, and finish stainless steel components. This method employs sophisticated software and automated tools for machining operations, including milling, turning, drilling, and grinding. The result is high accuracy and repeatability, crucial in manufacturing complex parts.
Stainless steel is an alloy consisting of chromium, iron and often nickel. Its unique properties like durability, corrosion resistance, and strength make it a preferrable across various industries. These characteristics allow stainless steel components to withstand harsh environments and high-stress applications, making them essential in critical engineering projects.
One of the features of CNC machining is its ability to deliver precision and accuracy. This technology enables the production of intricate designs and tight tolerances, vital in applications where performance and safety are paramount. Automating CNC machines reduces the likelihood of human error and increases production efficiency, leading to consistent quality in both small-scale and mass-production settings.
Additionally, CNC machines are highly versatile and can handle a wide range of stainless steel grades, from standard options like 304 and 316 to more specialized alloys. This adaptability allows manufacturers to produce simple, complex geometries tailored to specific application requirements. Typical applications include fittings, valves, medical devices, and structural parts, often demanding high precision levels and superior surface finishes.
Challenges and Solutions to CNC Machining Stainless Steel
Here are some of the common challenges and possible solutions to CNC machining steel:
Tool Wear and Breakage
Tool wear and breakage are significant challenges when machining stainless steel due to its hardness and toughness. The cutting tools can wear down quickly, leading to decreased cutting efficiency and the need for frequent replacements. This increases operational costs and can result in production delays if tools fail unexpectedly.
Solutions
To reduce tool wear and breakage, manufacturers can adopt several strategies:
- Use of Coated Tools: Employing cutting tools with advanced coatings, such as TiN (Titanium Nitride) or TiAlN (Titanium Aluminum Nitride), can significantly enhance tool life by providing a harder surface that reduces friction and wear.
- Optimizing Cutting Parameters: Adjusting the cutting speed, feed rate, and depth of cut can help reduce tool wear. Lower speeds and feeds are often recommended for CNC machine stainless steel to minimize heat generation and prolong tool life.
- Regular Tool Inspection: Implementing a routine inspection schedule allows for early wear detection, enabling timely tool changes before breakage occurs.
- Using Proper Tool Geometry: Selecting tools with the appropriate geometry, such as rake angles and cutting edge designs, can improve chip formation and reduce stress on the tool, leading to less wear.
Heat Generation
Heat generation during machining is another critical challenge when working with stainless steel. The friction between the cutting tool and the material can lead to elevated temperatures, causing thermal deformation and adversely affecting both the workpiece and the tool. Excessive heat can also accelerate tool wear and lead to workpiece distortion, compromising precision.
Solutions
Several methods can be employed to manage heat generation effectively:
- Cooling and Lubrication: Coolant systems, such as flood cooling or mist coolant, can help dissipate heat during machining. Proper lubrication also reduces friction, which can decrease heat buildup.
- Choosing the Right Cutting Speed: Slower cutting speeds may reduce heat generation but can also lead to increased tool wear. Finding the optimal speed that balances heat and efficiency is crucial.
- Implementing High-Pressure Coolant Systems: Using high-pressure coolant systems can enhance chip removal and cooling effectiveness, preventing heat buildup in the cutting zone.
- Advanced Tool Materials: Employing cutting tools made from materials that can withstand high temperatures can improve performance under high heat conditions and extend tool life.
Material Hardening
Material hardening is a phenomenon that occurs when stainless steel becomes harder during machining, particularly due to work hardening. This happens when the material is subjected to stress, leading to changes in its microstructure. Subsequent cuts can become increasingly difficult, causing tools to wear out fast and potentially leading to breakage.
Solutions
To manage material hardening effectively, manufacturers can consider the following strategies:
- Optimized Cutting Parameters: Using appropriate cutting speeds and feeds can help reduce the incidence of work hardening. Slower speeds can minimize the stress imposed on the material.
- Use of Cutting Tools with Specialized Geometry: Tools designed for machining hard materials can effectively cut through work-hardened layers without excessive wear.
- Employing Pre-Conditioning Processes: Pre-conditioning methods, such as annealing, can soften the stainless steel before machining, making it easier to cut and reducing the likelihood of hardening.
- Regular Tool Changes: Establishing a schedule for regular tool changes can help avoid the challenges associated with work-hardened material, ensuring that tools remain sharp and effective.
Surface Finish Quality
Achieving a high-quality surface finish is essential in many stainless steel applications. However, the material’s inherent properties can lead to surface irregularities, such as roughness or tool marks, which may necessitate additional finishing processes to meet specifications.
Solutions
To enhance surface finish quality during CNC machining of stainless steel, the following approaches can be beneficial:
- Fine-Tuning Machining Parameters: Adjusting feed rates and spindle speeds can help produce smoother finishes. Slower feed rates can lead to finer surface finishes by reducing the depth of cut per pass.
- Using Appropriate Cutting Tools: Selecting cutting tools specifically designed for finishing operations can help achieve better surface quality. Tools with a sharper edge and suitable coatings can minimize surface defects.
- Implementing Multi-Stage Machining: Employing a multi-stage machining process, where roughing and finishing operations are separated, allows for better control over surface quality.
- Post-Processing Techniques: After machining, finishing techniques such as polishing, grinding, or electropolishing can further improve the surface finish of stainless steel components.
Vibration and Chatter
Vibration and chatter during CNC machining can adversely affect CNC machine metal components’ surface finish and dimensional accuracy. These issues often arise due to insufficient rigidity in the setup, improper tooling, or high cutting forces, leading to instability in the machining process.
Solutions
To reduce vibration and chatter, manufacturers can implement the following strategies:
- Improving Machine Rigidity: Ensuring the CNC machine is calibrated correctly and rigid can help minimize vibrations. This includes checking for proper mounting and alignment of the workpiece.
- Optimizing Tool Path Strategies: Using optimized tool paths can help distribute cutting forces more evenly and reduce the likelihood of chatter. Strategies such as adaptive machining can be effective.
- Damping Techniques: Implementing vibration-damping technologies, such as using anti-vibration tool holders or damping materials, can significantly reduce the effects of chatter during machining.
- Selecting Appropriate Cutting Tools: Choosing tools designed to minimize chatter, such as those with specific geometries or materials, can improve stability and reduce vibration during cutting.
Tight Tolerance
Due to the material’s properties and the intricacies of the machining process, achieving tight tolerances in CNC machining of stainless steel can be challenging. Deviations from specified tolerances can lead to part rejection or require costly rework, impacting production efficiency.
Solutions
To ensure tight tolerances are met, manufacturers can adopt the following practices:
- Precision Machine Calibration: Regular calibration of CNC machines is essential for maintaining accuracy and ensuring that machines operate within specified tolerances.
- Using High-Quality Cutting Tools: Employing high-quality, precision-engineered cutting tools can help achieve better dimensional accuracy and maintain tight tolerances during machining.
- Implementing In-Process Measurement: In-process measurement systems, such as laser scanners or probe systems, can help monitor dimensions during machining and allow immediate adjustments.
- Conducting Thorough Pre-Production Planning: Careful planning and simulation of machining processes can help identify potential issues affecting tolerance levels, allowing for adjustments before production begins.
Conclusion
CNC machining of stainless steel presents unique challenges, including tool wear, heat generation, material hardening, surface finish quality, vibration, and the ability to achieve tight tolerances. These challenges can impact production efficiency and product quality, so manufacturers must adopt effective strategies to overcome them.
Manufacturers can significantly enhance machining using optimized cutting parameters, advanced tool materials, and effective cooling techniques. Implementing regular inspections, pre-conditioning methods, and multi-stage machining can further contribute to improved outcomes. Additionally, investing in high-quality machinery and employing real-time measurement systems ensures that precision is maintained throughout production.